How ERP Can Prevent Downtime in High-Volume Manufacturing
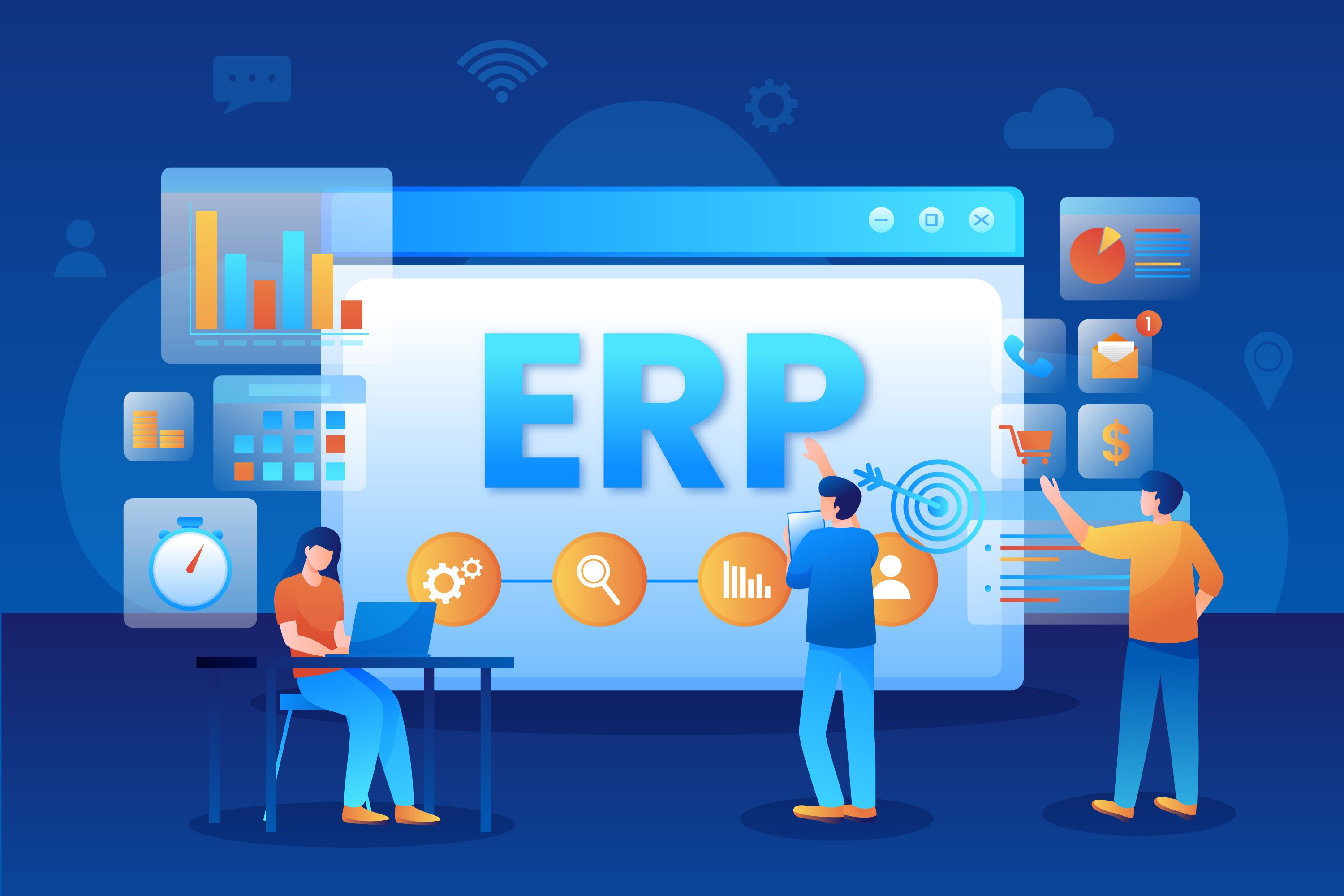
Photo by freepik @ freepik
Production facilities operating at high volume rates encounter downtime as a serious operational risk that reduces their performance and financial returns. Machine downtime and process delays during operation result in reduced revenues and operational expenses while causing missed deadlines. Most downtime can become foreseeable and minimised when manufacturers implement appropriate organisational systems. ERP software designed for manufacturing is a critical operational tool for maintaining product flow efficiency throughout operations.
This may interest you: From Purpose to Flow: Operational Excellence in Action
Manufacturing ERP software developed for modern applications provides tracking abilities for inventory, orders, and additional functions. ERP platforms unite every element of production, including material starting points, equipment maintenance, personnel organisation, and scheduling. ERP systems achieve this through their provision of real-time visibility, centralised data, and improved departmental communication, which helps manufacturers detect problems early to avoid downtime. For operations managers who want to boost output and minimise waste, it is necessary to understand the ERP systems' methodology for decreasing interruptions.
Production Planning and Scheduling
Inadequate scheduling practices are the leading cause of high-volume production stoppages. Machine scheduling issues that involve either too much or too little work can result in operational problems such as equipment jams, empty machine time, and fast-paced production that produces faulty items. ERP production planning systems use intelligent tools to connect equipment availability resources with employment scheduling, material supply management, and delivery functions. Such features prevent manufacturers from executing duplicate orders and optimise resource usage across equipment.

ERP systems allow users to dynamically reschedule operations. The program automatically adjusts operational schedules when unexpected problems occur, such as delayed materials or labour shortages. Teams can direct work toward alternative machines or move labour resources to different duties instead of interrupting production. Dynamic scheduling enables operations to function smoothly even when inflexible production plans fail because of high-volume work pressures.
Inventory and Material Management
The absence of required materials represents a familiar reason for downtime to occur. The unavailability of required raw materials during the right time period causes production lines to stop operating. ERP systems prevent such events by tracking inventory exactly and using automated reordering features. Continuous monitoring of stock and consumption data by this software enables providers to schedule supply orders before inventory runs low.
ERP systems create a connection between procurement functions and production requirements. The system uses current production plans instead of historical prediction data to guide purchasing decisions. Materials arrive at the right time because this process eliminates both supply shortages and excessive inventory, resulting in operational disruptions.
Maintenance and Equipment Monitoring
Equipment failures that appear suddenly have the power to cause total shutdowns in high-volume manufacturing operations. ERP systems equipped with maintenance management features stop failures through their ability to monitor equipment use, automate preventive maintenance tasks, and track service records. The proactive maintenance approach lets manufacturers perform preventative actions instead of simply repairing equipment after breakdowns, thus they can minimise unexpected downtime when machines stop working.
ERP systems achieve superior proactive maintenance capabilities when Internet of Things (IoT) devices connect with their system infrastructure. The integration of sensors on machines enables real-time data acquisition of temperature conditions, vibration measurements, and performance standards into the ERP system. By utilising these metrics, production facilities can detect equipment degradation and substandard performance, allowing managers to schedule maintenance services and thus continue production activities.
Workforce Coordination
Human workers stand equally vital for maintaining manufacturing production stability with their counterparts, materials, and machinery—the shortage of departmental coordination, together with unclear labour status, results in time delays. Manufacturing ERP software solutions for manufacturing operations enable human resource management to create and schedule worker deployment according to production demands, thus placing staff members correctly when needed.
ERP systems feature a built-in platform that maintains employee training information and qualifications. The employees receive proper assignments for particular machinery or procedural tasks through the manager's oversight. Staffing mistakes result in safety risks and poor quality, and create delays from process discrepancies and errors that may occur during reassignments on the shop floor. A productive workforce that applies coordinated placements forms an essential basis for achieving uninterrupted production operations.
Real-Time Data and Visibility
Decision-makers who lack prompt system data cannot address situations before production cuts occur. ERP systems maintain a common platform that displays real-time insights about production activities from various business areas. The platform integrates all essential information, including materials assessment, machine operational data, and employee work schedules, alongside current order development. The solution process starts when issues become visible through this platform, so they get resolved before turning into major problems.
Read more: 5 Tools To Maximise ERP Operational Efficiency
ERP systems incorporate a feature set which alerts users about vital situations such as inventory depletions and upcoming machine maintenance deadlines. The immediate alert system gives managers the ability to respond instantly at a time when managing problems later causes operational disruptions. The need for fast organisational responses becomes vital because small operational delays cause significant negative effects in high-volume manufacturing operations.
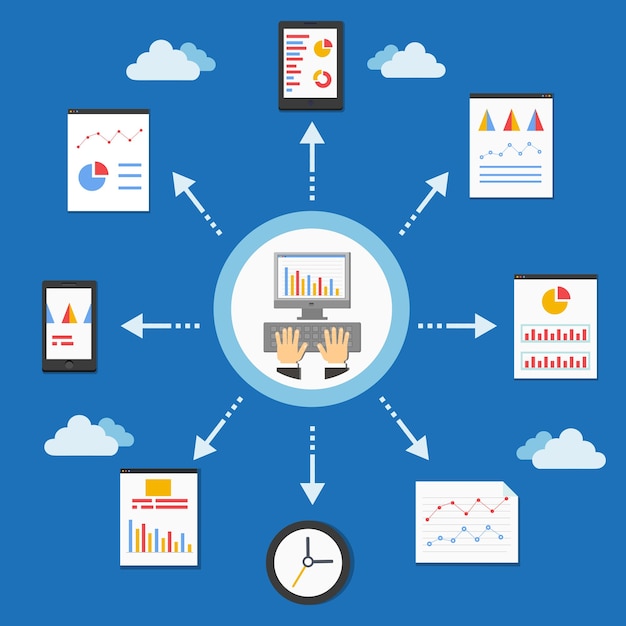
The continuous downtime problem in high-volume production exists despite available solutions for its resolution. Every production element achieves heightened structure while developing enhanced visibility and proactive management through ERP systems. Manufacturing ERP software enables businesses to schedule assets better and handle materials while preserving machines and staff to help them identify and solve issues that create production delays. Companies that select and use their ERP system effectively will minimise production disruptions, which allows them to safeguard their earnings while defending their market standing.
Leaderonomics.com is an advertisement-free website. Your continuous support and trust in us allow us to curate, deliver, and maintain our website. When you support us, you enable millions to continue reading for free on our website. Will you give it today? Click here to support us.
Business
Tags: Alignment & Clarity, Artificial Intelligence, Building Functional Competencies, Business Management, Consultant Corner, Digital
AMRYTT MEDIA LLC is the team behind GUESTPOSTLINKS.NET, a trusted platform for high-quality guest posting services. For any inquiries, feel free to contact us at hello@guestpostlinks.net or call 17196002784.